- 5005 Aluminum Block
- 5052 Aluminum Block
- 5083 Aluminum Block
- 5086 Aluminum Block
- 5182 Aluminum Block
- 5454 Aluminum Block
- 5754 Aluminum Block
- 6061 Aluminum Block
- 6063 Aluminum Block
- 6082 Aluminum Block
- 1060 Aluminum Block
- 2024 Aluminum Block
- 2A12 Aluminum Block
- 7005 Aluminum Block
- 7075 Aluminum Block
- 3003 Aluminum Block
NEWS
INFORMATIONTel:
86 17344894490aluminium cnc blocks
Last Updated :2023/06/13
Introduction of aluminium cnc blocks
Product name:aluminium cnc blocks.
Material: 1070, 2024, 2A12, 3003, 5052, 5083, 5086, 6061, 6063, 7075, etc.
Specifications: customized processing according to customer samples or drawings.
Process: Aluminum blocks can be finely cut, punched, drilled, machined, etc.
The specifications of aluminium cnc blocks
Thickness: 8-500mm
Width: more than 200mm width or according to customer requirements
Length: within 16m or according to customer requirements
Packing: standard export cartons and pallets, or according to customer requirements
The features of aluminium cnc blocks
1) Can be arbitrarily cut: according to customer requirements, can be arbitrarily cut, the cut surface is smooth.
2) Paper can be stuck between protective film or aluminum block.
3) Flat surface, no burr in the incision
The Usage of aluminium cnc blocks
aluminium cnc blocks are widely used in electronics, machinery, molds, precision machining etc fields,
Product name:aluminium cnc blocks.
Material: 1070, 2024, 2A12, 3003, 5052, 5083, 5086, 6061, 6063, 7075, etc.
Specifications: customized processing according to customer samples or drawings.
Process: Aluminum blocks can be finely cut, punched, drilled, machined, etc.
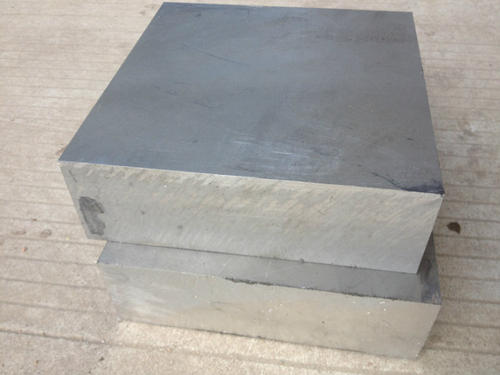
The specifications of aluminium cnc blocks
Thickness: 8-500mm
Width: more than 200mm width or according to customer requirements
Length: within 16m or according to customer requirements
Packing: standard export cartons and pallets, or according to customer requirements
The features of aluminium cnc blocks
1) Can be arbitrarily cut: according to customer requirements, can be arbitrarily cut, the cut surface is smooth.
2) Paper can be stuck between protective film or aluminum block.
3) Flat surface, no burr in the incision
The Usage of aluminium cnc blocks
aluminium cnc blocks are widely used in electronics, machinery, molds, precision machining etc fields,